El carisma de Mariano no pasa inadvertido, él sonríe, juega, interactúa con sus compañeros, los saluda con un choque con el puño de su mano biónica, la misma que le sirve para compartir objetos y apoyarse en sus actividades cotidianas.
Este niño de 10 años, oriundo de San Ramón de Alajuela, a pesar de haber sufrido una amputación en su brazo derecho, disfruta de su clase favorita que es educación física, destaca por sus buenas calificaciones y participa de eventos escolares como desfiles y bailes.
Gracias a una prótesis totalmente electrónica, Mariano tiene una vida activa.
Se trata de una pieza fabricada a partir de impresiones 3D y que le permite a Mariano realizar los movimientos de forma intuitiva.
La pieza que incluye hombro, codo y mano cuenta con sensores adheridos a la piel que perciben los estímulos de los nervios para que pueda tener movibilidad.
Esta prótesis fue elaborada por el ingeniero electrónico, Adrián Quesada, quien dirige Proyecto Oportunidad, organización que ya puso a andar 25 prótesis biónicas.
Esta empresa aprovecha los alcances de las impresiones 3D para que el costo de fabricación se reduzca. Por ejemplo, una prótesis elaborada por Quesada puede costar entre $400 y $4.000, mientras que las comerciales pueden superar los $20.000 (cerca de ¢11,37 millones).
Vea la galería de fotografías
Estas no son las únicas prótesis fabricadas en el país, el Tecnológico de Costa Rica (TEC) y Avant Biomedical, son otros laboratorios en donde se está apostando por esta innovación.
Aunque el desarrollo y las investigaciones de estas piezas continúan, el nicho de las prótesis está listo para ser uno de los más revolucionarios en Costa Rica.
Los ingenieros y científicos nacionales están claros en que, con la ayuda de estas tecnologías, se agilizarán los tiempos de entrega y se abaratarán los costos de las prótesis, pues actualmente se debe pasar por un proceso largo para obtener una de estas a través del Estado.
La Caja Costarricense de Seguro Social (CCSS) tiene algunas casas ortopédicas en las que se distribuyen las prótesis bajo receta, pero estas tienen listas de espera y no son los suficientemente cómodas ni modernas.
Por esta razón, los emprendedores además de contribuir con estas invenciones, también han explorado un potencial en su comercialización, y es en este punto en el que compañías e instituciones se han mostrado interesadas.
La demanda existe, pero las posibilidades para adquirirlas son limitadas.
La respuesta a las creaciones son positivas y el Centro Nacional de Rehabilitación (Cenare), casas ortopédicas y laboratorios médicos son algunos casos de organizaciones que están anuentes a realizar alianzas.
Pieza por pieza
Las impresiones en 3D favorecen la creación de estas prótesis debido a la facilidad de producción y la reducción de costos.
Otras de las ventajas más significativas que brinda esta tecnología son que se evita la importación de los componentes y que las medidas para cada prótesis son más detalladas y exactas.
Miguel Araya, ingeniero en diseño industrial de Ergo Tec, explicó que la impresión 3D resulta más económica porque en lugar de tener que extraer y desechar material para acoplar una pieza, se puede utilizar el material justo para crear la prótesis.
Además, se abre espacio para realizar mejores diseños, se ajusta a las características anatómicas del paciente y se acelera el proceso de fabricación, al tiempo que reduce la posibilidad de error al moldear la pieza.
La impresión 3D permite hacer prótesis más personalizadas y se adapta mejor a cada cuerpo en función de la ergonomía.
Quesada concuerda con esos criterios, porque las 25 prótesis que ha elaborado han sido con base en la impresión 3D.
Según el ingeniero, esta técnica les permite escalar con facilidad y concretar una idea nueva en cuestión de horas.
Además de la técnica, las prótesis biónicas también necesitan de otros materiales que les permita ser más eficientes.
Proyecto Oportunidad utiliza procesadores rápidos, sensores de temperatura, luz, giroscopio e incorpora un módulo de Bluetooth Low Energy.
Son fabricadas con plásticos especiales que son libres de contaminantes y resistentes al agua.
LEA: Tico desarrolla la primera prótesis biónica a partir de impresiones 3D en Costa Rica
Entre las mejoras que han incorporado en sus últimos modelos están las transmisiones de Titanio y la incorporación de motores más eficientes.
Estos ingenieros trabajan no solo de la creación de la pieza, sino también en ofrecerle al paciente una experiencia de comodidad y de eficiencia.
“Lo que estamos buscando principalmente es bajar los costos, pero también trabajar con la parte emocional. Usualmente las prótesis existentes son muy tubulares, se adecúan a ciertas necesidades funcionales pero no por completo a las necesidades emocionales que tiene un paciente que ha sufrido una amputación”, explicó Araya.
En el caso de Proyecto Oportunidad, cuentan con un sistema de apadrinamiento con el que otras personas pueden hacer donaciones y empresas desde su área de responsabilidad social pueden aportar para la fabricación de más prótesis.
En el 2016 contaron con 135 padrinos que costearon 17 prótesis para personas de recursos económicos limitados. También tienen un modelo de ventas tradicional.
Atención en los detalles
Otro laboratorio que trabaja por el desarrollo de prótesis de calidad es Avant BioMedical, startup enfocada en el campo de la biotecnología.
David Meléndez, de Avant BioMedical, explicó que en esta compañía se enfocan en la parte de investigación y desarrollo y han trabajado tres prótesis.
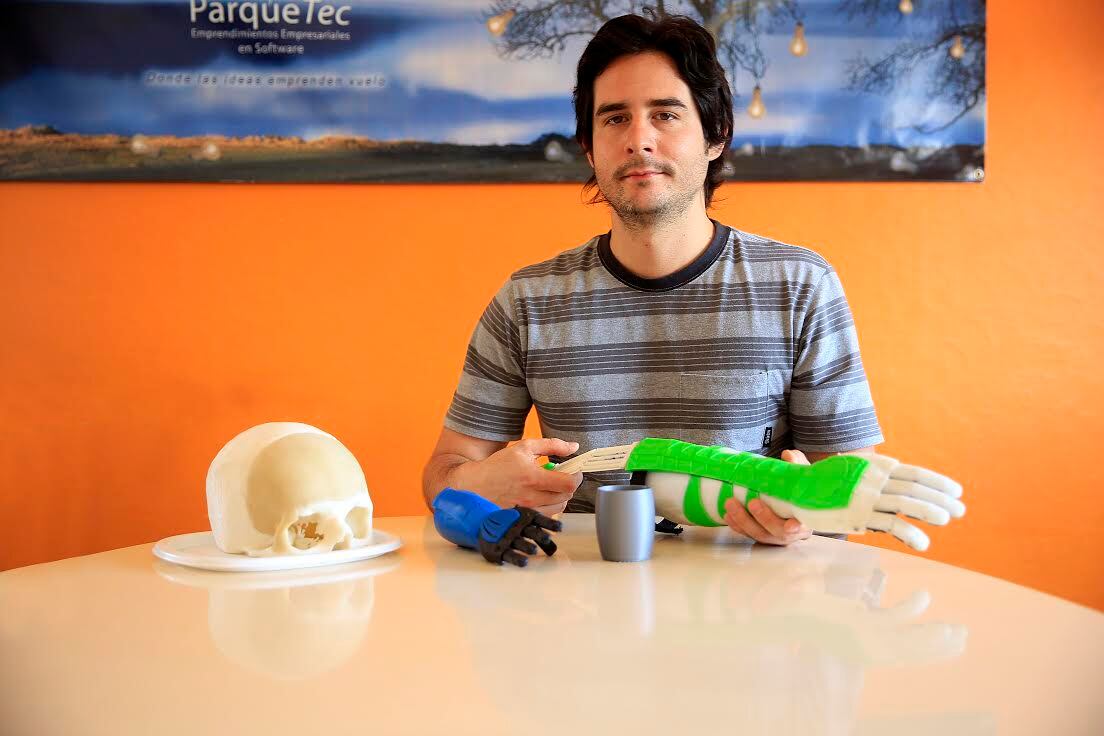
Este laboratorio se apoya en el diseño, la impresión en tercera dimensión y el escaneo en alta tecnología para crear implantes de sustitución ósea.
Meléndez dijo que se encargan de realizar prótesis personalizadas, por lo que cuando hay un defecto óseo, o una lesión por un accidente, se hace el diseño exclusivo del implante.
LEA: ‘Startups’ de biotecnología exploran su alto potencial
La prótesis se fabrica en titanio, en un material sintético o en plástico, todos tolerados por el cuerpo humano.
La empresa espera en un mediano plazo trabajar como una fundación y en unos dos meses poder desarrollar una tecnología ortopédica de bajo costo.
Creando nuevas oportunidades
Otra institución que está explorando y desarrollando la creación de prótesis en Costa Rica es el TEC desde su Laboratorio de Ergonomía Aplicada (Ergo Tec).
Según Miguel Araya, ingeniero en Diseño Industrial del TEC, todavía no están fabricando las prótesis, pero sí se encuentran trabajando en un proyecto de investigación relacionado con el diseño y desarrollo de prótesis transtibial (para pacientes amputados abajo de la rodilla) implementando tecnologías de manufactura aditiva y escaneo 3D.
Este proyecto se inició en el 2016 y exploran tecnologías de manufactura aditiva, materiales, así como el diseño y aspectos de ergonomía y biomecánica.
Se espera que el trabajo avance hasta llegar a otras etapas como la validación y luego que pueda ser implementada en personas que necesiten de una pierna.
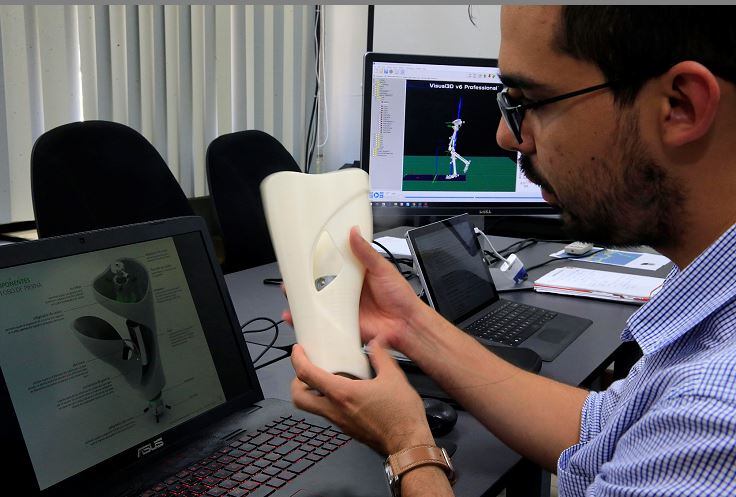
Mano a mano
Como las opciones se han diversificado y resultan ser buenas apuestas por la calidad de los productos que se están diseñando en el país, ya hay instituciones que se han mostrado interesadas en realizar alianzas y proyectos de la mano de estos emprendedores.
Por su parte, Avant BioMedical también ha estrechado lazos con Establishment Labs, para el uso de impresoras 3D y también han participado en proyectos con el Hospital de Niños y sostienen conversaciones con el Cenare y con el Taller de Prótesis de la CCSS.
En el caso de Proyecto Oportunidad, las casas ortopédicas han sido buenas aliadas y, según Quesada, gracias a ellas se ha logrado mejorar y validar sus modelos.
También facilitaron que sus pacientes hayan sido valorados por un especialista previo a la fabricación de la prótesis, con el fin de asegurarse de que no van a causar ningún problema a corto, mediano o largo plazo.
“Hoy en día tenemos pacientes de la CCSS y del Cenare usando nuestros modelos, y esperamos que esta cifra aumente en los próximos meses”, afirmó Quesada.
Proyecto Oportunidad aprovechó el sistema de apadrinamiento que precisamente es con el que Mariano se benefició para obtener su brazo biónico.
Ahora este niño ramonense usa su prótesis que le sirve de apoyo para actividades cotidianas con movimientos sutiles y naturales.
Mientras no la está utilizando la apaga, luego la vuelve a encender y así sucesivamente.
Con una sola carga, esta pieza le puede durar para más de cuatro horas de uso.
Como Mariano está en etapa de crecimiento, la prótesis que utiliza actualmente deberá de ser ajustada dentro de aproximadamente un año y medio. Aunque los ajustes serán mínimos, ya que la parte eléctrica está instalada y lista para que el niño pueda sacarle el mayor provecho.